5 Keys to Warehouse Rack Labeling
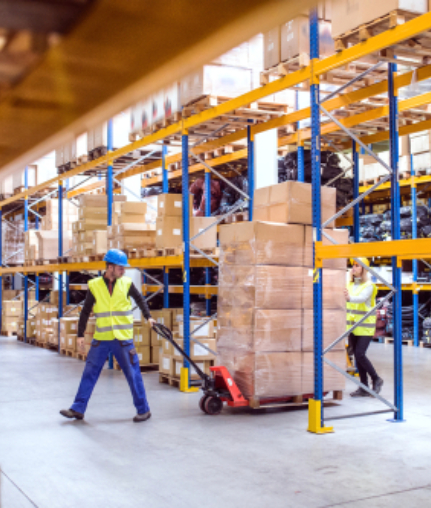
5 Keys to Warehouse Rack Labeling
There are millions of square feet of warehouse racks in the world, and while some are only rarely used, many are utilized for high-speed operations on a daily basis. This is why there is no universal way of laying out the floor plans for a warehouse, for putting warehouse rack labels to use, and even selecting warehouse labels themselves. Instead, there are different methods used to:
1) Identify racks – As an example, consider the many ways that sections or units of shelving can be positioned to hold gear. There might be a single, elongated unit or many smaller, single units. It often depends on issues like product size, the numbers of SKUs at work, the variations in products, and more. The goal is to identify racks with unique IDs or attributes within sections, and not by the entire rack itself
2) Label from ground up – It makes good, old-fashioned common sense to place numbers on racks from the bottom up. In other words, rows closest to the floor will receive the lowest numbers, and so on and up. Most will also opt to use warehouse rack labels with double digits, i.e., 01 rather than 1 on its own to help with clarity and make it easier to manage expanding numbers of shelves or units.
3) Grid or serpentine layout – When envisioning a warehouse and making plans to use warehouse labels most effectively with racks, it is essential to decide how the layout will be done. When a warehouse has to address the issue of picking and packing orders strategically, the layout of the racks is best done in the curving style known as serpentine. When the warehouse rack labels don’t have to be selected based on such factors as picking requirements, an entirely different set of criteria can be used in their selection and design.
4) Signage – Warehouse labels can be what are known as long-range, and this can be a style that is accomplished through placards with highly visible barcodes or through warehouse rack labels that are simply long-range barcode labels themselves, and not signage. As an example, an overhead, reflective placard may be more suited to bulk storage areas while the smaller warehouse labels work best for individual segments or units.
5) Determine the ideal warehouse labels – This is one of the most complex issues of warehouse rack labeling, and many companies opt to include the maker of their warehouse rack labels in their planning teams. After all, it is possible to choose from a variety of materials, sizes and designs.
At Express, identification is made simple through an array of warehouse labels suitable to any sort of racking and picking solutions. There are the essential long-range barcode placards already mentioned, but there are also multi-level rack labels, long-range labels, magnetic labels (for metal pallets and racks), floor tabs for bottom-up labeling, and even specialty frames.
Think of Express as a partner in the warehouse rack process, and utilize their fast turnaround quotes and competitive pricing to identify your best options in warehouse rack labels.