Best Practices Guide: Leak Detection and Repair (LDAR)
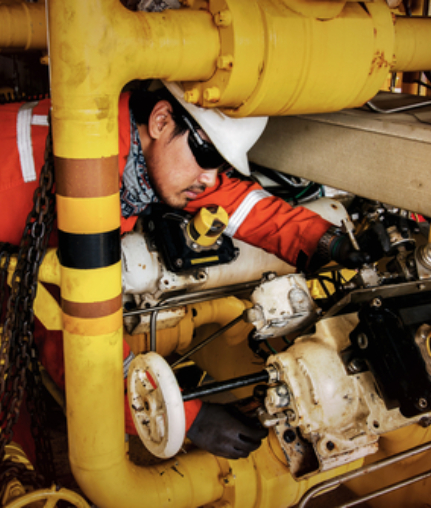
Best Practices Guide: Leak Detection and Repair (LDAR)
Due to the emission of volatile hazardous air pollutants by leaking machineries or equipment, such as connectors, valves and pumps, the Environmental Protection Agency (EPA) thought it wise to enact the Leak Detection and Repair (LDAR) system in order to identify and repair leaking equipment or machines in chemical manufacturing and petroleum refining industries. The LDAR system procedures, like the Method 21 analyzer calibration and monitoring procedures are to be followed by specifically selected technicians and managers to curb the emission of these volatile organic compounds (VOCs) emitted by the industrial machinery.
LDAR Definition
An LDAR is a procedure program instituted by the Environmental Protection Agency (EPA) to control the emission of volatile hazardous air pollutants (VHAPs) and volatile organic compounds (VOCs) emitted from some industrial equipment. It is a procedure program used by facilities for leak detection and repair of leaking equipment or machinery that include; connectors, valves, pumps, agitators and compressors, thereby, minimizing the emission of these VOCs and VHAPs. The EPA ensures operation and application of the LDAR program in many chemical manufacturing and petroleum refining industries, and due to the implementation of the EPA program, different sizes of facilities have been successfully reviewed.
Why Regulate Equipment Leaks?
Accordance to the findings gotten by the EPA, it was stated that the release of VOCs and VHAPs in the atmosphere is as a result of leaking industrial equipment, such as steam traps, valves, connectors, and the likes. Also, the amount of air pollutants emitted by these types of machinery is around 70,367 tons each year of VOCs and approximately 9,357 tons each year of VHAPs. The findings also state that the emission of these gases contributes largely to the formation of ozone on ground-level, which is one primary contributing factor of smog and respiratory disease, especially in children and asthmatics. Some other supposed problems caused by the emission of these air pollutants are; birth defects, cancer, and reproductive effects. Many locations in the United States, especially those areas where these pieces of machinery are used do not get up to the National Ambient Air Quality Standard (NAAQS) for ozone. Some very frequently emitted VHAPs include benzene, naphthalene, xylene, chloride, toluene, acetaldehyde, methylene, and formaldehyde.
Sources, Causes and Control of Equipment Leaks
Several sources are responsible for the emission of hazardous air pollutants from industrial machinery. Here are some major sources/causes of equipment leaks:
- Pumps – function as transporters of fluids
- Valves – valves acts as a control to the flow of the fluids
- Connectors – connectors are used to merge process and piping machinery
- Compressors – these components are responsible for the increase in pressure of the fluids
- Pressure Relief Devices – they are designed to prevent equipment from going above its normal working pressure
- Open-ended Lines – these lines are hoses or pipes that are open to the surrounding environment
All the stated components can cause the release of these harmful gases in one way or another. For example, the leaks from valves often take place when there is a failure in valve O-ring or packing.
Control of Equipment Leaks
The curbing of the emission of these VHAPs due to leaking equipment can be done through the implementation of the LDAR tags or by customizing/changing leaking machines with ‘Leakless’ components. Usually, leaks caused by compressors, open-ended lines, and sampling connections can be tackled by just customizing the machine or component. Also, the use of valve tags, stream trap tags, sealless pumps, and leakless valves can minimize or completely put an end to leaks in industrial equipment or machinery.
Benefits of an LDAR Program
The EPA estimated about 63% of the emission of VHAPs from leaking equipment could be reduced by implementing the LDAR program. According to the EPA, chemical manufacturing industries could control the emission of VOCs up to 56% by employing the use of LDRA programs. Here are five benefits of implementing an LDAR program:
- Minimization of product losses in chemical manufacturing and petroleum refining industry
- Maximized safety of workers and operators in facilities
- Reduction in the exposure to hazardous gases for the neighbouring community and employees
- Potential reduction in emission fees of the facility
- Lessens the need for setting Compliance and Enforcement National Properties for harmful air
Essential LDAR Planning Steps / Elements
Seeing that the emission and leak detection and repair program is pretty complex in nature, facilities can follow these five basic steps/elements in carrying out the implementation of an LDAR program:
Identifying Components
It is necessary for each regulating component to have a specific ID number and identified the location. A machinery log containing information on newly added equipment, equipment is taken out, and replacement parts should always undergo maintenance. Also, using ID tags on the various components can go a long way in identifying components.
Leak Definition
The unit for measuring leak definition is parts per million (ppm). It is the measurement of the concentration that has gone beyond the accepted threshold of relevant regulations. There are different levels of accepted thresholds in a different state and federal regulations, and the accepted threshold is based on the industry. Due to the confusion, multiple regulations may pose in a particular facility. The EPA suggests that defining leaks should be at a lower level compared to the standard threshold of every applied regulation.
Monitoring Components
According to the EPA, the acceptable method used to monitor components leak detection purpose is the EPA Reference Method 21. This method periodically assesses the weekly, monthly, quarterly, or annually emission of air pollutants.
Repairing Components
Repairing components require regulatory guidelines in order to fix a deadline by which the component responsible for the leak is to be fixed. This deadline can range between a few days and many weeks. But it is recommended that detected leaks should be repaired within the first five days after leak detection and within fifteen days after every failed attempt. The facility can apply other regulations set accepted repair practices like packing gland nuts or tightening bonnet bolts. And if properly documented and warranted, the equipment can be placed on a DOR (Delay of Repair) list if the equipment needs to be shut down before repair can take place.
Recordkeeping
It is required in LDAR regulations that a huge amount of information on each regulated part be documented and preserved by the right information. The use of an Asset Management system will make data collection less expensive, faster, and more precise.
Implementing all five elements will reduce the man-hour requirements as well as overhead costs, which will, in turn, minimize complexity and ensure compliance. The compliance cost of a facility can be reduced by employing the asset management system to focus on automatic capturing of data with leak detection and repair tags.
Method 21 – Volatile Organic Compound Leaks
The application of the Method 21 – Volatile Organic Compound Leaks of the EPA regulations will help facilities determine the leaking of VOC from process machinery. The primary sources of leaks include, but are restricted to, flanges, valves, pumps, connections, compressors, process drains, pressure-relief devices, open-ended valves, dressing vents system of the compressor and pump seal, agitator seals, access door seal and accumulator vessel vents.
Yielding to the necessities of the Method 21 will improve the information derived from air pollutant sampling practice.
Method 21 helps in classifying and locating leaks only. It’s not a method used for the straight measurement of mass emission ratio gotten out of separate sources.
Identifying / Monitoring Components
The following can be employed in facilities to identify or monitor components and prevent leaks in equipment or machinery:
Unique Barcoded LDAR tag
Unique Barcoded LDAR tag functions as a monitoring tool for repairmen and field technicians. Using the barcoded LDAR tags, they can monitor the rate at which VHAPs and VOCs are emitted from process equipment used in various chemical manufacturing and petroleum refining processes. LDAR technicians can successfully monitor and conform with the regulations of the EPA if they follow the LDAR monitoring techniques and calibration procedures duly.
Potential Leak Sources
Several sources are responsible for the emission of hazardous air pollutants from industrial machinery. They include:
- Flanges, valves, pumps, connections, compressors, process drains, pressure-relief devices, open-ended valves, dressing vents system of the compressor and pump seal, agitator seals, access door seal and accumulator vessel vents.
All the stated components can cause the release of these harmful gases in one way or another. For example, the leaks from valves often take place when there is a failure in valve O-ring or packing.
Repair
Repairing components require regulatory guidelines to fix a deadline by which the component responsible for the leak is to be fixed. This deadline can range between a few days and many weeks. But it is recommended that detected leaks should be repaired within the first five days after leak detection and within fifteen days after every failed attempt. The facility can apply other regulations set accepted repair practices like packing gland nuts or tightening bonnet bolts. And if properly documented and warranted, the equipment can be placed on a DOR (Delay of Repair) list if the equipment needs to be shut down before repair can take place.
Recordkeeping
It is required in LDAR regulations that a huge amount of information on each regulated part be documented and preserved by the right information. The use of an Asset Management system will make data collection less expensive, faster, and more precise.
Implementing all five elements will reduce the man-hour requirements as well as overhead costs, which will, in turn, minimize complexity and ensure compliance. The compliance cost of a facility can be reduced by employing the asset management system to focus on automatic capturing of data with leak detection and repair tags.
Essential Technology
- Labels – Mobile Printers or Custom Printers
- Scanners
- Inventory Management System
Benefits of Properly Implemented LDAR Program
Here are five benefits of a properly implemented LDAR program:
- Maximized safety of workers and operators in facilities
- Lessens the need for setting Compliance and Enforcement National Properties for harmful air
- Minimization of product losses in chemical manufacturing and petroleum refining industry
- Potential reduction in emission fees of the facility
- Reduction in the exposure to hazardous gases for the neighboring community and employees