10 Things to Know About Warehouse Location Mapping
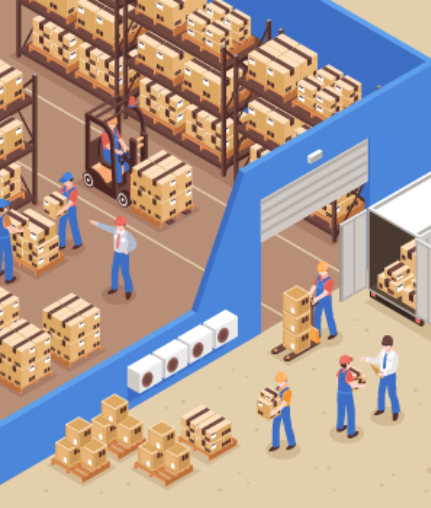
10 Things to Know About Warehouse Location Mapping
Manufacturers, shipping specialists, and retailers all use warehouse facilities, and most have a system for warehouse location mapping in place. However, some may not realize the value (in time and money) that a solid warehouse inventory management system provides. That is why it is essential to develop a custom warehouse location system and make unique plans for warehouse location mapping based on your needs.
#1 What Is Warehouse Location Mapping?
Of course, these terms, like warehouse inventory management, a warehouse location system, and warehouse location mapping, may all be unfamiliar to you. Essentially, each translates to the same thing and boils down to naming and identifying the many shelf and unit positions, travel paths and routes, and work areas within any warehouse facility.
A good way to envision or understand warehouse inventory management is to think of the individual locations of each product (whether it is a large product on a palette or a group of them taking up an entire section of shelving) as having an “address”. Just like a person has a home address with street, city, and zip code, a warehouse location system defines the position of products in the same way. There are the aisles that might be major highways or streets, and shelving units that are homes (or in the case of the “from the bottom up” style of warehouse location mapping, shelves that are similar to apartments).
Once you visualize these multi-dimensional grids that work horizontally and vertically, it becomes easier to understand a warehouse inventory management system. It gives a coded location where products live until picked and packed for shipment or delivery. Of course, a warehouse location system is also suited to long-term storage, drop shipping ventures, and more.
#2 The Planning Within Any Warehouse Location Mapping Solution
One vital element of warehouse inventory management is the labeling that is used throughout, and many experts will turn to the makers of their labels as partners in the design process. They will review the options in warehouse labels to be sure that the best solutions are put to use.
#3 Consider Pre-Planning and Labeling
Any plans will be based on available floor space, the type of picking done, and whether it will be foot traffic or foot and vehicles. The potential bottlenecks can be avoided by doing paper and pen planning, but most firms use warehouse location mapping as the ideal answer, laying it out and identifying the most efficient spaces for items.
#4 Evaluating Anticipated Traffic
While mapping out the space available is important, it will be inefficient if not done using the anticipated traffic patterns. For example, will the layout be grid-like or facilitate lots of movement and use a serpentine style? Will there be a need to get strategic in layout, or will back and forth movement be acceptable?
#5 Easy Addressing
We already noted that the mapping is exactly like everyday mapping and gives addresses or locations to specific goods. How are you going to provide smart location names for the specific items or product categories? After all, those names and designations have to take into account the amount of picking to be done, the volume sold, the size of the goods, and so on.
#6 Forget “Over Labeling”
There is one important and easily overlooked rule to warehouse mapping, and that is the tendency to try to under label, i.e., simplify labels. The truth of the matter is that you cannot over label inventory or stock. The unique names, zones, categories, and codes you give to even the smallest product grouping will facilitate the mapping, organizing and managing processes.
#7 Follow Common Patterns
Another easily overlooked rule is to skip the usual traffic or flow patterns. Labels should always work from top to bottom and left to right. Change that pattern and your warehouse staff may struggle.
#8 Don’t Forget “Other” Zones
Warehouse mapping has to take into account the various zones or regions apart from storage. Remember that will probably be a space needed to organize the invoices and handle assembly, shipping, and also receiving and sorting. Don’t get so overzealous that you forget to a lot space for other key functions.
#9 Consider Integration
Not all warehouse mapping and labeling will work with the software used for warehouse management. Take the time to ensure that all of the plans fit together as snugly as puzzle pieces, and work with solutions provided by the label manufacturer.
#10 Work with a Flexible Label Maker
The best efforts to label clearly can be thwarted by low-quality and underperforming labels. Express offers an array of warehouse barcodes that make labeling and mapping easier than ever. Their range of products includes:
- Long Range Barcode Placards – Scannable from up to 50 feet away, they are retroreflective placards with high visibility and the capabilities of featuring custom design. They are ideal for larger warehouses where bulk storage is done on entire units rather than items in single sections.
- Long Range Barcode Labels – Also capable of being read from up to 50 feet away, and made of the same retroreflective materials, they are highly visible labels capable of customized sizes and designs, and work well when entire units or sections are put to use storing similar items in larger facilities.
- Multilevel Rack Labels – Experts always advise that a warehouse location mapping solution use “bottom-up” numbering. In other words, the lowest levels have the lowest numbers and the highest shelves have the highest numbers. The best multilevel rack labels facilitate identification of rows, aisles, bays, and so on. They are color-coded and will work as stickers or placards with the option for customization.
- Magnetic labels – When customizable, they can make relocation of inventory or stored items much easier and should be strongly magnetic.
- Pallet labels – These should feature adhesive backing or holes for mounting and affix directly to pallets made of polyester or aluminum.
- Floor tags – These are footers placed on the floors in front of palettes and are strong enough to withstand warehouse foot traffic. They should be scannable and customizable for the best outcomes, as well as being available in steel or aluminum. Frames or holders also are key components.
A warehouse location system is nothing to take lightly, and the ten tips here are ideal for helping any business to map out, organize, manage and use a warehouse or multiple sites efficiently.